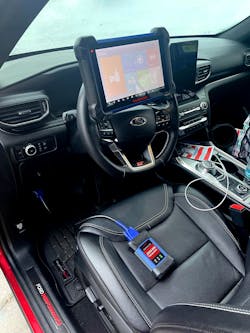
The changes in programming with regard to Chrysler vehicles are well-known. Less known are Ford’s network changes. The changes were subtle at first but have evolved in complexity and sophistication, so much that, in my opinion, Ford’s networks now surpass those of other domestic and Asian manufacturers and come just short of the those designed by European automakers.
Before jumping into tools and protocols, by which vehicle modules communicate either with other modules or with scan tools, I want to discuss the onboard diagnostics (OBD) port, now known as OBD-II, and what some of the 16 slots control. (See the accompanying diagram.) Not all Fords have all 16 slots filled. Depending on the year and other factors, they might not have all the applicable networks.
Although each vehicle manufacturer has the right to make the OBD port as it sees fit, some requirements are standard. These are known as the SAE standards, for SAE International. Pin 16 is always constant battery power. This is direct from the battery, with only a fuse protecting the circuit. Pin 4 is always a ground to the chassis, and pin 5 is a signal ground. The only common network across all vehicles is pins 6 and 14, referred to as the Control Area Network or CAN. If the vehicle has CAN, communication will take place on pins 6 and 14.
The Old Days
Ford’s first original-equipment tool was the New Generation Star (NGS). This tool started as an OBD-I tool and advanced to OBD-II. The giant capital-T-shaped tool is unmistakable. It used the same PCMIA cards (software memory cards) as the Tech2. Many seasoned locksmiths got one of these, because it was the only machine for a long time to perform passive anti-theft systems (PATS) functions. It was slow and had a small screen.
The tool worked well on the Standard Corporate Protocol (SCP) network. This network is known as J1850PWM in the SAE world. SCP used pins 2 and 10. This network was well-designed and ahead of anything else at the time. It was a two-wire network that allowed serial communication to the modules. It worked a lot like CAN. If one leg of the network were broken, the network would continue to communicate. However, the data rate was just 41.6 kilobits per second (kbps). To put the system’s slowness in perspective, dial-up internet speed was 56 kbps.
Naturally, programming pre-CAN Ford keys or modules was hampered by computer and internet speed. Ford made the switch to CAN from 2003 to 2007. The reason so many newer programming tools struggle with this system is because they’re too fast for the Pre-CAN system to handle.
The only odd part about the SCP network setup is the Flash EEPROM Programming Signal (FEPS), which is pin 13 on the OBD-II port. It’s nothing more than an 18-volt signal to the powertrain control module (PCM) to allow the module to accept the new programming. The FEPS circuit continued to be the Ford PCM programming system for years after. Even as Ford advanced through various CAN styles, FEPS remained. So, if you get a FEPS error when trying to program a PCM, it often is an error between the J2534 tool on pin 13 and the PCM.
Starting in 1996, Ford tried to move from the NGS to the World Diagnostic Solution (WDS). This was a tablet-based tool running Windows. It was big and bulky and not well-received, so it was more or less shoved aside and the NGS retained. However, a problem arose in 2003 when CAN came around, because NGS never was able to handle CAN. To account for that, the Vehicle Communication Module tool (VCM I) was created with a cradle to help with CAN on the NGS.
In 2004, Ford then moved to its Integrated Diagnostic System (IDS) with the VCM I. This software remained in place for years and now is being phased out. The IDS had 95 percent of the function coverage. The only missing coverage was air suspension in 2004 and earlier, which requires NGS and a special cable to connect.
One of the biggest advantages of the CAN is how fault-tolerant it is. Almost all CAN modules are in parallel, instead of series. Parallel systems work like Christmas lights that remain lit even if one bulb is out. Parallel means that if a module were unplugged or it died, the rest of the network would continue to operate. Another advantage is that CAN’s developer, Bosch, continues to improve the network. Bosch made advances that took the original protocol to a speed of 125 kbps.
Moving Forward
The next step Ford took was to eliminate the clutter. By this, I mean Ford added another CAN to allow critical modules to talk with each other faster. The basics of how the modules communicate is this: A module sends a request for information. Then, every module responds in order, either answering the request or making a request from a different module.
Ford’s medium-speed CAN changed a few things, including putting the body-control and powertrain systems on separate networks. Meanwhile, the development of high-speed CAN increased network speed to 1 megabit per second — three times faster than original CAN. Body-control systems use medium-speed CAN, while critical systems use high-speed CAN.
Around the time of this network development (2008), Ford replaced the VCM I with the VCM II — same software, better hardware.
The last major network change was the introduction of the gateway module. No, this is NOT like Chrysler, not yet at least. Ford went to a gateway, because it required more than two networks, and the data link connector (DLC) port was filled by rules.
To circumvent these rules, Ford turned the DLC into the gateway. The gateway has 24 wires as inputs from the vehicle, which the gateway translates to the 16-pin port DLC. This allows for up to nine different CANs. Ford knew it would want these additional networks for safety features, such as front radar, lane departure and blind-spot detection.
This gateway presents a challenge, however. When a scan tool is connected to the vehicle, it isn’t connecting to the network, so the tool has access only to the data the gateway wants your tool to have. This makes diagnosing the network problems without the Ford special breakout box exceedingly difficult.
You might wonder why we’re explaining the networks. The first reason is to help you to learn something you might not have known about networks. The second is because when Ford makes a network change, it also seems to make a PATS change.
Let’s start with the first network system, SCP. In SCP networks, all the security is in the PCM. This was a simple system with a PATS transceiver and the engine control module (ECM). The key is read by the transceiver, which then sends the information directly to the PCM.
As we entered the CAN era, the PATS module now was in the instrument cluster or with the PCM. This means that when you program a PCM vehicle, you only have to perform a module sync. You don’t have to do anything with the keys. If you work with the anti-theft module or cluster, then you have to have two keys.
A PCM requires only a parameter reset, which is a module sync. The anti-theft module learns all the module IDs that are installed to allow it to start. Each module has a unique ID, and the anti-theft module learns these so the vehicle can’t be stolen through a simple swap out of the vehicle computer. The system requires two keys to be programmed to the anti-theft module. So, if the customer were to lose a key, you could add a single key and the vehicle would start. If a used cluster (which is the PATS module) were installed, a key must be added, and the module would require a parameter reset.
It’s important to note that in CAN vehicles, when the cluster and PCM don’t communicate, the mileage is displayed as dashes. The ECM being offline from the cluster will cause the anti-theft light to blink, which indicates an immobilizer error. Many assume that it’s a key problem — it isn’t. Remember, the anti-theft system is now in the instrument panel cluster (IPC) module, and because of the module sync, we have to have a PCM, IPC module and a proper key for a happy immobilizer system.
Although the key isn’t in the ECM, it still is necessary to satisfy the anti-theft module. I often see a failed PCM relay as the root cause of the problem. When the relay doesn’t latch on, the PCM doesn’t get power and, thus, can’t communicate with the rest of the modules in the vehicle. This is where the Autel MaxiIM IM608 can be used to perform a scan and troubleshoot the problem. Access the IMMO function, and the tablet will display the PCM as unable to communicate. While the PCM is offline, the anti-theft system will display as nonfunctioning.
The Road Ahead
The next generation is the current gateway generation, which moved security from the cluster to the body control module (BCM). Now, when a BCM is replaced, it has to be programmed and reset; two new keys have to be programmed; the tire-pressure monitor system has to be relearned; and then, finally, a BCM self-test has to be performed to wrap up programming. The vehicle dome light will blink until all these steps are completed.
The BCM is one of the most complex modules in a Ford vehicle. It has all the networks in and out of it. This module is known to have hundreds of lines of code for the as-built data. The nice part is, Ford has made only small changes recently. And it ditched the 600-second wait in favor of entering one’s National Automotive Service Task Force Vehicle Security Credentials (formerly known as the locksmith identifier passcode). This is a game-changer. I perform a lot of parameter resets, and those 10 minutes really add up.
The last major change is seen in the brand’s newest vehicles and systems. As I stated previously, IDS is being phased out, and new software is taking over. The Ford Diagnostic and Repair System was introduced in 2018.
However, in 2020, Ford had a new problem as a result: The reliable VCM II no longer was fast enough, so Ford released the VCM3. Although almost everything is the same, one major difference is the tool’s CAN-FD (Flexible Data-Rate) protocol. CAN-FD makes high-speed CAN look like dial-up. Why would Ford make such a change? Ford wanted a faster network for the numerous new modules it added to its latest vehicles.
That’s where we are now. The bottom line: The development of Ford vehicle communication networks and the effect this has had on key and immobilizer programming simply can’t be addressed in one article. I look forward to discussing the advancements of Ford and other vehicle manufacturers in an upcoming issue.
Matthew Skundrich is the owner of Mobile Advanced Diagnostics & Programming in Orlando, Florida. He has worked as an automotive diagnostician for more than 15 years.