How to Deploy a Key System the Right Way: Deploying the System
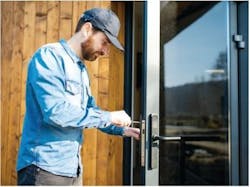
This is the fourth in a five-part series focused on How to Deploy a Key System the Right Way.
Now that we defined the scope of our project, identified crucial participants (stakeholders), created the project plan and designed our masterkey system as well as our key management program, it’s time to think about the deployment of our key system.
We’ll start by placing an order with the manufacturer.
Prevent Order Delays
Manufacturers report that more than half of key-system orders placed by locksmiths lack the proper documentation or contain discrepancies. This often causes delays in order processing, because the manufacturer has to go back to the locksmith for clarification.
To avoid delays in the manufacture of your key-system order, be sure to provide the following:
A key-control agreement. As discussed in the third article of this series, key-control agreements are issued by the key manufacturer and signed by the locksmith, the end user and the manufacturer. The agreement outlines the utility patent on the key system and seeks to ensure that only the approved locksmith has legal rights to produce keys to operate the locks.
If the signed key-control agreement doesn’t accompany the order, the manufacturer likely will suspend processing of the key system until the agreement is furnished. What’s more, experience has shown that if the agreement requires approval by the end user’s legal department, the order can face significant delays.
A keying schedule. You might recall discussion of the site survey in article two. The site survey lists each door in the project and captures the details of each opening, including door hardware specifications, whether it’s a right-hand or left-hand opening, the lock finish and how many cylinders are required for each door. It also denotes each lock’s identity within the masterkey hierarchy. The site survey will prove indispensable in creating the keying schedule that will be provided to the manufacturer.
A keying schedule template typically is furnished by the manufacturer to capture the specifications of the key-system order. It outlines how all cylinders are to be keyed and the quantities, markings and shipping instructions for all keys and cylinders that constitute the order. If this schedule is incomplete or inaccurate, it can significantly affect order manufacturing and, thus, the overall deployment schedule, so be sure to double- and triple-check the keying schedule.
In addition, when conducting a final review of order paperwork, be sure the purchase order provided to the manufacturer matches the keying schedule’s quantities and parts numbers exactly. Although this might seem obvious, many orders incur delays because of inconsistencies between the purchase-order summary and keying-schedule line items.
Plan the Staging Area
A new key system can involve a significant investment and, depending on the size of the installation, might require days or even weeks to complete. Before the key system arrives on site, it’s important to consider how to protect it from theft and unauthorized access. Be sure to discuss staging options with the client to ensure that all components, including cylinders, keys and key blanks, can be held in a secure, lockable area upon delivery. This might be a single room, a container, a trailer or a similar space.
As a best practice, when the shipment arrives — well before installers begin working — inspect all order components to be sure quantities, model numbers and required finish are correct. Also, check to be sure keys are marked and customized as expected and functioning properly in their respective locks.
Devise an Installation Plan
The smoothest installations are usually the result of thorough planning, particularly when conducting large installations. Whether your project involves 10 doors or 10,000 doors, a well-planned methodology certainly will make the project run more smoothly.
In article two, we discussed creating a detailed work plan. This plan outlines the expected sequence of installation for all locks and cylinders. Will installation begin on the first floor or on the third floor? This will influence how product should be arranged in the staging area. Most manufacturers clearly label individual boxes with door numbers that correspond to the keying schedule to facilitate product identification. Understanding the installation plan will enable you to organize boxes in the order in which installers will want to access the products.
Monitor Installation Quality
In article one, we discussed the value of having a quality-control plan in place. Designing the System is covered in article two. Article three covers Developing the System.
As work gets underway, the project manager, or another appointed individual, should bear responsibility for monitoring the progress and quality of work.
Quality audits should result in a punch list that captures any unresolved product discrepancies or installation issues that must be addressed before the project is deemed complete. Is a key not functioning properly? Is a cylinder not seated correctly? A well-documented checklist shared with the client representative will help to instill confidence that the deployment is being monitored closely and can be a helpful tool to ensure the project meets customer expectations.
In the final article in this series, we will explore Phase 5 of How to Deploy a Key System the Right Way, what we have termed the fifth “D” – dialogue. It will outline the value of ongoing customer service to your business and include best practices to discuss warranties and preventative-maintenance options with customers.
Dale L. Bowman, CML, CPP, PSP, PCI, LEED BD+C, is Medeco’s Director of Business Development, OEM and International Sales.
Deployment Phase Highlights and Action Items
- Be sure to submit the key-control agreement along with the key-system order to the manufacturer. If necessary, verify that the key-control agreement has been reviewed and approved by the client’s legal professionals.
- Carefully review order documents to avoid delays in order processing by the key-system manufacturer. Before sending the keying schedule to the manufacturer, compare it with details of the site survey and correct any inaccuracies.
- Ensure the purchase order corresponds to the keying schedule’s quantities and parts numbers exactly.
- Define a staging area in which to secure key-system components before and during installation.
- Upon arrival, compare items received against the purchase order. Conduct a spot check to be sure keys function as expected.
- Review the planned sequence of installations and arrange products in the proper order in the staging area.
- Conduct regular quality audits during installation, and maintain a list of items to be completed before the project is finalized.
Dale L. Bowman
Dale L. Bowman, CML, CPP, PSP, PCI, LEED BD+C, is Medeco’s director of business development, OEM and international sales.